Table des matières
What if you could reduce waste, increase efficiency and deliver more value to customers? The answer lies in Lean manufacturing. It sounds like an uphill battle, but with the right Lean manufacturing tools, driving out waste is easier than you might think.
5 Lean Manufacturing Principles
Lire le livre blanc • 5 Lean Manufacturing PrinciplesAgilePlace Free Trial: AgilePlace Online Kanban Software
Sign up for a 30-day free trial and you and your team can start building online Kanban boards today. Experience for yourself how AgilePlace supports continuous delivery initiatives, eliminates waste and improves your team’s delivery processes and speed.
Commencer votre essai gratuit • AgilePlace Free Trial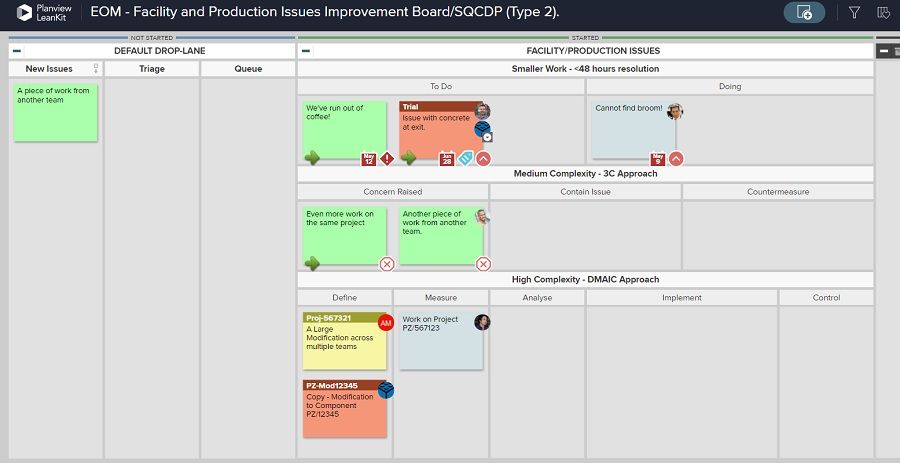
Here are useful Lean manufacturing tools you need to get started.
Lean Manufacturing Tools to Jumpstart Your Efforts
Whether you’re building a physical product or creating a Lean culture, it helps to have the right tools for the job. Think of this article as a toolbox, from which you can pick and choose the right tools to use in your organization.
Some of them are techniques for managing people and some are frameworks for solving problems, while others offer ways of thinking about or structuring work. All these Lean tools are intended to help you drive out waste, increase efficiency, and make the most of your resources.
PDCA problem solving cycle
The first Lean tool we will discuss is the PDCA cycle, a Lean management tool used to operationalize continuous improvement.
PDCA stands for Plan-Do-Check-Act (sometimes Plan-Do-Check-Adjust) and provides a holistic framework for identifying and solving problems quickly. Included in the PDCA cycle are the following steps:
- Plan for a specific goal
- Do the work required by that plan
- Check the results of the work
- Act / Adjust to fix any unsatisfactory results
When using PDCA as one of the Lean manufacturing tools in their arsenal, some people include an “O” step (for Observe) at the beginning of the cycle, to emphasize the need to understand the current realities of a situation before jumping into “solutionizing.”
PDCA is intended to be a cyclical process–a four-step loop (or five, if you include the O step) that is repeated continuously. It can be particularly helpful when:
- Starting a new improvement project
- Developing a new process, product, or service
- Defining a repetitive work process
- Implementing any change
- Implementing continuous improvement
The Five Whys
Root cause analysis is an important concept in Lean manufacturing, because it helps teams continuously refine their processes to eliminate sources of waste. Without a framework for structuring these analyses, however, teams often don’t dig deeply enough to truly uncover root causes–instead, stopping at more surface-level issues and working to resolve them.
The Five Whys is a simple but effective thinking tool that helps make sure that they are accurately identifying true root causes.
Quite simply, it requires participants to continually ask “why?” questions (typically five or fewer times) to peel back the layers. This questioning allows teams to diagnose problems without any statistical analysis and often identifies multiple root causes and the relationships between them.
Whether or not the Five Whys is used along with other Lean manufacturing tools, it’s a highly versatile thinking tool that can be used on its own in a variety of situations. For examples and use cases of the Five Whys, we recommend this article.
Gemba
Gemba is a Japanese word that translates to “the real place.” In Lean, it refers to the place (physical or digital) where work is being done–like the shop floor in a manufacturing facility. Going to the Gemba is a way of getting to the heart of where value is created–a call to leaders to get out of their offices and spend time on the plant floor to gain a thorough and accurate understanding of the realities of their working environments.
All too often, decisions about manufacturing value streams are made without consulting the people on the front lines, those who might have the most insight about how to improve processes and resolve issues.
When problems arise, it’s important to go to the Gemba to observe what is happening and make thoughtful decisions that accurately reflect the reality of the problem. The Gemba is one of three important Lean manufacturing tools that can help leaders approach their role with greater humility as they sharpen their analytical skills.
Jidoka (Autonomation)
Jidoka is another Lean manufacturing tool of Japanese origin. It translates to “intelligent automation” or “automation with a human touch” and is a way of maintaining quality control in a semi-automated environment.
Jidoka, or autonomation, involves designing equipment to partially automate the manufacturing process, so that machines can automatically detect defects when they occur, and stop the line so that a human can address them.
The purpose of this Lean tool is to prevent the production of defective products and eliminate overproduction. It also reduces labor costs by eliminating the need for direct human supervision over every station on a production line. With a partially automated system, workers can monitor multiple stations, and focus their attention on resolving problems instead of simply monitoring for quality.
Andon
Most Lean manufacturing tools emphasize the importance of visualizing important information and empowering the entire value stream to act upon that information. Andon, or the “Andon cord” is a Lean tool that does both.
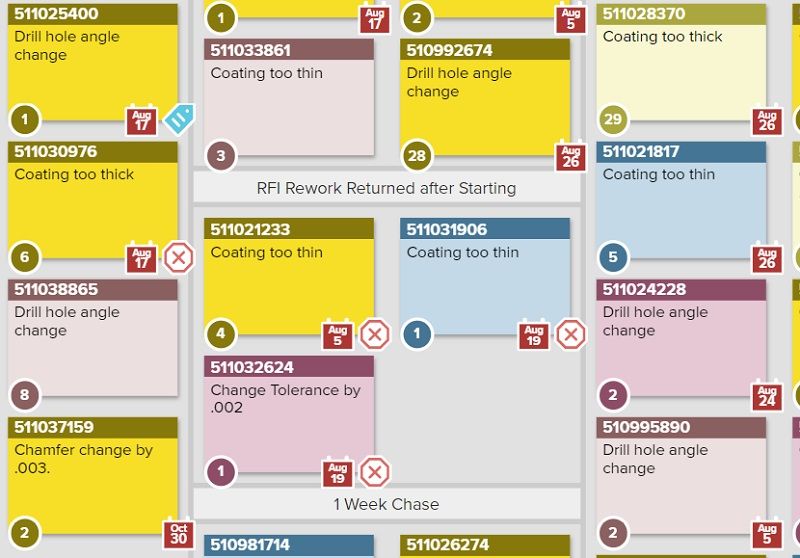
t’s a visual feedback system that indicates production status and empowers operators to stop the production process when issues arise – this is called “pulling the Andon cord,” in reference to early systems which used a physical cord to allow operators to stop the production line. (Think of a line in a public bus that you can pull to request the bus to make an unplanned stop.)
Modern Andon systems vary in design, but often involve the use of colored lights, audio signals, text, or other displays to indicate status.
The use of Andon systems is a key part of Just-in-Time manufacturing. By empowering anyone on the line to quickly identify and address issues without waiting for management, manufacturing lines can be more self-sufficient and resolve issues in real-time.
This also encourages everyone on the line to participate in Kaizen (continuous improvement) – because people are more empowered to innovate when they can call out and effect change.
Continuous Flow (aka one-piece flow)
Continuous flow is a Lean manufacturing tool that involves using smaller batch sizes to increase the speed and efficiency of production. Continuous flow refers to the state of continuously, consistently delivering outputs by moving each item through each step of the process, instead of processing items in batches.
Think of it as making pizza: Making one pizza from start to finish – rolling the dough, assembling the toppings, and baking the pizza – and serving the pizza when it’s ready is continuous flow. Rolling out the dough for, let’s say nine pizzas, then assembling the toppings on all nine pizzas, and then baking all nine pizzas – all before being able to serve just one pizza – is delivering in a batch.
Conceptually, it might sound as though delivering outputs one item at a time might be slower than delivering in batches. Practicing continuous flow allows manufacturers to deliver value to their customers more frequently and with fewer delays.
Producing in smaller batches also allows teams to regularly examine the output to make any necessary improvements for the next batch, thereby eliminating waste.
Cellular manufacturing
Cellular manufacturing supports continuous flow by calling on teams to arrange workstations based on the parts they produce in order to minimize travel time for those parts and allow for rapid feedback across stations about any issues.
Together, these two Lean manufacturing tools also enable teams to produce smaller, more efficient batches. Organizations typically achieve cellular manufacturing by arranging workstations in a “U” formation.
Five S (5S)
5S is another of the Lean manufacturing tools focused on workstations. It’s a step-by-step method for organizing, cleaning, and maintaining orderly working environments to maximize efficiency, improve safety, and reduce waste.
In their original Japanese, the five steps of the 5S system each begin with the letter S, which is where the system gets its name: Seiri, Seiton, Seiso, Seiketsu, Shitsuke. These terms have been translated into English, conveniently also all beginning with the letter S:
- Sort (remove any unnecessary materials)
- Set in order (arrange materials so they are easy to find and access)
- Shine (clean the workspace regularly)
- Standardize (make the previous three Ss a standard routine)
- Sustain (institute regular audits)
For a more in-depth explanation of the 5S Lean system and how to implement it, we recommend this article.
Total Quality Management (TQM)
This Lean tool, and the following one, work together as the key operational activities of a quality management system. Total Quality Management refers to organization-wide efforts to install and maintain an environment where employees continuously improve their ability to produce high-quality products on demand.
The word “total” refers to the fact that departments outside of production (such as sales, marketing, accounting, engineering, and design) are equally responsible for actively managing and improving quality in their operations as well–not just those on the production floor.
Total Productive Maintenance (TPM)
Total Productive Maintenance (TPM) is a Lean manufacturing tool that aims to increase operational efficiency of equipment and safety for workers. While TQM focuses on continuously improving the quality of products being produced, TPM focuses on increasing the volume of production by maintaining the reliability of equipment.
Increasing production volume isn’t simply a matter of working faster—because when speed increases, equipment deteriorates faster, creating a greater risk of error and potentially creating more waste.
Increasing production volume is achieved by increasing Overall Equipment Effectiveness, or OEE, which we’ll explain in the next section.
TPM blurs the roles of production and maintenance by empowering operators to help maintain their equipment. The goals of TPM are to achieve a state of perfect production, which means:
- No breakdowns
- No small stops or slow running
- No defects
- No accidents
The 5S system is the foundation of TPM. The 5S system is a useful Lean manufacturing tool that creates a work environment that is clean and well-maintained. There are eight supporting activities of TPM that build upon this foundation:
- Autonomous Maintenance: Places the responsibility for regular maintenance of equipment into the hands of operators.
- Planned Maintenance: Uses predicted and / or measured failure rates to schedule maintenance tasks.
- Quality Maintenance: Design error detection and prevention into standard production processes.
- Focused Improvement: Form cross-functional teams to proactively identify and act upon opportunities for continuous improvement.
- Early Equipment Management: Use practical knowledge and understanding of equipment gained through TPM to design new equipment.
- Training and Education: Work to proactively identify and fill in knowledge gaps necessary to achieve TPM goals; includes operators, maintenance team members, and managers.
- Safety, Health, and Environment: Target the goal of an accident-free workplace, eliminating potential health and safety risks.
- TPM in Administration: Apply TPM techniques to administrative activities to address waste in administration.
Overall Equipment Effectiveness
Part of TPM is the Overall Equipment Effectiveness (OEE) metric, which measures the percentage of working time that is productive.
OEE is based on scores for availability, performance speed and output quality. Multiplying these three numbers gives the OEE metric, with an 85% best-in-class for organizations using Lean manufacturing tools, a 60% average for organizations using Lean manufacturing tools, and a 40% average for organizations not embracing any Lean manufacturing tools.
Takt time
Takt time is one of the Lean manufacturing tools focused on measuring customer value. It measures the average rate at which teams must manufacture products to meet demand.
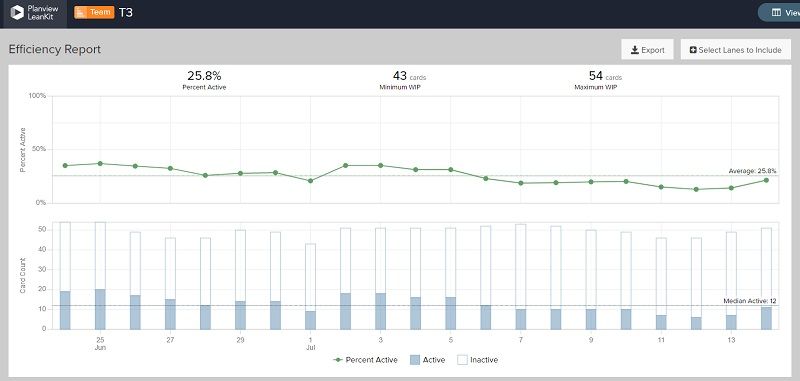
To calculate takt time, divide the working time available for production (in hours, days, weeks) by the units required to meet customer demand. Using this Lean manufacturing tool, if a team works 40 hours a week and the company expects customers to buy 80 units a week, the takt time is 0.5 (40 / 80). This means the team must produce one unit in half an hour to meet customer demand.
Standardized work
Standardized work and takt time are two Lean manufacturing tools that work together. Specifically, standardized work helps teams achieve their takt time by creating and documenting a set, repeatable process for how teams should function. For example, it documents the steps teams should take, the materials they need, and the time required for each step.
Mistake proofing
Mistake proofing focuses on detecting mistakes as they occur (either automatically through technology or manually through inspection) and notifying workers accordingly. Like all Lean manufacturing tools, it helps eliminate waste and increase efficiency, this time by surfacing errors as they occur to prevent defective parts from moving further down the process.
Leveling the workload
Leveling the workload calls for teams to manufacture products consistently despite inconsistencies in customer demand. That means even though customers might buy 100 units one week and 60 units the next week, teams should maintain a consistent output over a set period of time (e.g. a week or a month). This consistency helps teams remain efficient since they do not need to switch setups to manufacture different products in unpredictable patterns.
Embracing Lean Manufacturing Tools
Embracing Lean manufacturing tools like those outlined above can go a long way toward helping your team increase efficiency and reduce costs. Most importantly, these Lean manufacturing tools can help you deliver a higher quality product to customers in a faster and more predictable way – a win for both your operations and your customers.