Table des matières
The term Lean manufacturing refers to the optimization of the practices, processes, and habits used by knowledge workers – more specifically, using Lean principles to work smarter, innovate faster, and deliver more value to customers. If you’re looking for practical tips on how to implement Lean manufacturing in your organization, you’ve come to the right place.
AgilePlace Free Trial: AgilePlace Online Kanban Software
Sign up for a 30-day free trial and you and your team can start building online Kanban boards today. Experience for yourself how AgilePlace supports continuous delivery initiatives, eliminates waste and improves your team’s delivery processes and speed.
Commencer votre essai gratuit • AgilePlace Free TrialPremiers pas avec la méthodologie Lean
Le Lean est un état d'esprit qui vous accompagne dans la prise de décisions plus judicieuses sur la façon dont vous investissez votre temps, votre énergie et votre argent.
Consulter l'e-book • Premiers pas avec la méthodologie Lean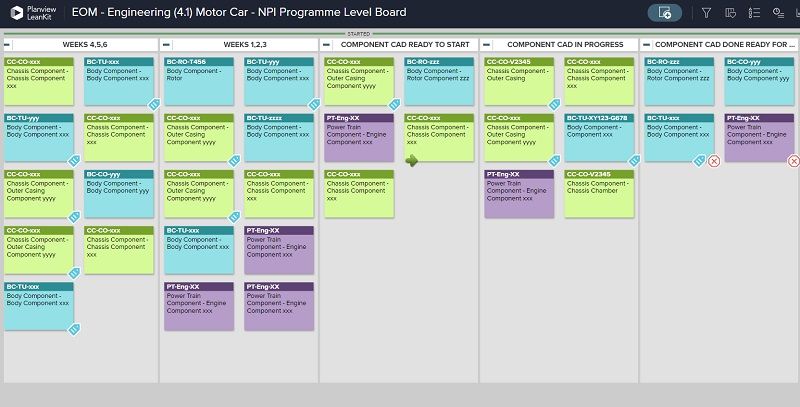
It’s important to note that picking and choosing a few Lean practices or principles won’t make your organization Lean. Lean experts (and esteemed authors of The Machine That Changed the World) Jim Womack and Dan Jones emphasize that in order to truly realize the benefits of Lean manufacturing, we have to rethink the entire organizational model.
“If individual breakthroughs can be linked up and down the value chain to form a continuous value stream that creates, sells, and services a family of products, the performance of the whole can be raised to a dramatically higher level,” they wrote. Achieving this state, the Lean enterprise, begins with creating a vision for the entire organization as a Lean system.
The First Steps of Lean Manufacturing
Realizing the benefits of Lean manufacturing – improved efficiency, flexibility, and customer responsiveness – starts with gaining alignment across the organization. These are the first steps we recommend for any organization wanting to implement Lean manufacturing at scale.
Find Your Why
Teams and organizations usually know what they do. They understand how they do it – but why? That’s a tougher question to answer – but a critical one.
As Simon Sinek explained in his widely popular TED talk, understanding the why behind your actions is the single most important factor for success, in virtually anything – at home, at work, and in life. It’s also critical when adopting a new way of thinking, which is what implementation of Lean manufacturing is, at its core.
If you’re going to convince everyone in your team, department, or enterprise that they need to change the way they fundamentally think about work, you’ll need to be able to explain why.
Why is your organization undergoing this change? Is it to reconnect with your customers, become more innovative, reach profitability, thrive in the future global economy? Figure out what that reason is for your organization (and socialize it heavily), and you’ll be infinitely more likely to implement Lean manufacturing successfully.
Recognize and Address Conflicting Needs
Through years of research studying Lean manufacturing organizations (as well as Lean enterprises in other industries), Womack and Jones articulated that in order to practice Lean production at the enterprise level, organizations need to recognize and satisfy three needs:
- The needs of individuals: Individuals need to be able to keep and enjoy their jobs
- The needs of functions: Organizations need to be organized by function to maintain and grow organizational knowledge; but truly agile organizations need people to organize into cross-functional teams
- The needs of companies: Companies need to be able to calculate costs and analyze benefits by activity, and therefore value control over agility / Lean-ness
In traditional organizations, it’s nearly impossible to meet all three of these needs and maintain a high level of agility – conflicts between the three needs inevitably have a negative impact on the organization’s ability to be Lean.
Luckily, as more companies have worked through these challenges, new solutions have emerged that enable enterprises to achieve a favorable balance between “individual opportunities, functional strength, and the well-being of member companies,” the authors share. Lean portfolio management refers to the application of Lean thinking to managing enterprise, program, and product portfolios to help organizations meet all three needs.
Find a Champion (or Become One)
Depending on the culture of your organization, adopting a Lean practice might be a gutsy move. It’ll have everyone in the organization pushing back on things, questioning things, and saying, “No” more. It may involve making difficult decisions in the interest of reducing waste. A visible, vocal champion of Lean – someone who will celebrate wins, facilitate discussions, and inspire others to continue onward – can be critical to overcoming the challenges involved in making transformative cultural shifts.
If your organization is adopting Lean from the top-down, then you’ll likely have support for your new, continuously improving behavior. But if your implementation of Lean manufacturing is part of a grassroots effort, you’ll need help.
If your Lean champion is someone already in an executive leadership position in the organization, it can do a great deal to bolster your Lean initiative and increase its odds of “sticking.”
In fact, in over 3,000 Lean practitioners surveyed, we found that the highest-performing Lean teams had an executive champion 69% of the time.
Make your executive champion’s job easier by keeping them informed: Share your learnings regularly, use data to demonstrate growth, share engaging articles about Lean, invite them to sit in on standups and retrospectives. If you’re championing a team, get involved and learn as much as you can about Lean manufacturing principles, so you can truly practice Lean leadership.
Master the Basics
Although the concepts behind Lean production are simple, they can be challenging to implement in our complex, ever-changing work environments. Learning to think, respond, and act in a Lean way requires you to retrain your brain–and at first, the Lean way can seem counterintuitive.
Strengthen your Lean muscles by reading Lean books to learn theory and principles. Learn about Lean manufacturing tools and techniques and practice adopting them in your own work. Foster Lean education in your teams by hosting “lunch and learns” and creating forums where people can share their experiences, ask questions, and learn together.
Many organizations find success in bringing in external Lean coaches to launch their Lean implementations. Lean coaches can facilitate workshops, answer questions, share resources, and guide your teams to sustainable success with your Lean implementation.
Map Your Value Stream
Once you feel comfortable with Lean manufacturing principles and practices, engage in a value stream mapping exercise.
The purpose of a value stream mapping exercise is to help you understand how value flows through your team and your organization.
Going through the exercise will provide lots of opportunity for important, clarifying conversations that will help you begin to effect change in a positive way.
Use Kanban to Bring Your Value Stream to Life
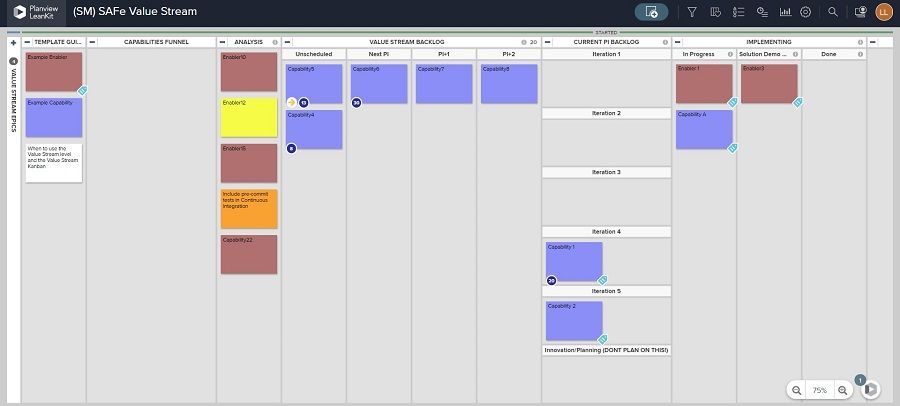
Also originating from the Toyota Production System is the practice of Kanban, a visual workflow management tool that can help provide accountability and structure to your Lean initiative.
Value stream mapping will help you identify the steps in your process; Kanban will help you analyze and optimize that process for value creation. If you’re looking for a pragmatic, hands-on approach to implementing Lean, we highly encourage you to complete the five exercises contained within the Kanban Roadmap.
Foster a Culture of Experimentation
Why is failure bad? In traditional work environments, we’re taught that failure represents a waste of time, energy, and money. Failure is a risk that did not pay off.
But as smart and talented as our employees are, they will fail. Failure is an inherent part of innovation – so if we discourage failure, we discourage innovation. The Lean manufacturing approach embraces and even celebrates failure as an opportunity for growth.
The goal isn’t to eliminate failure, but to mitigate the impact failed ideas have on the system.
We do this by:
- Failing early and often
- Testing our ideas before scaling them
- Asking customers for feedback on new ideas, and only investing in the ones that stick
Innovative companies aren’t those who get it right every time. They’re the ones who experiment, learn, and make informed decisions faster than their competitors. They reduce the impact of failure by seeking it out, rather than running from it. Fostering a culture of experimentation is an essential first step towards becoming more innovative, more influential, and more profitable.
The How: Lean Tools
You know your why, and by learning about Lean principles, you’ve learned the what of Lean. Now it’s time to learn how to practice Lean. When it comes to practicing Lean day-to-day, it’s helpful to have some practical tools in your arsenal.
Before we wrap up, we’d like to share some of the most helpful Lean tools you can start using to transform the way you work. We’ve learned that the most successful Lean implementations rely on the following tools:
- TABLEAUX KANBAN
- WIP limits
- Livraison continue
- Pull system
TABLEAUX KANBAN
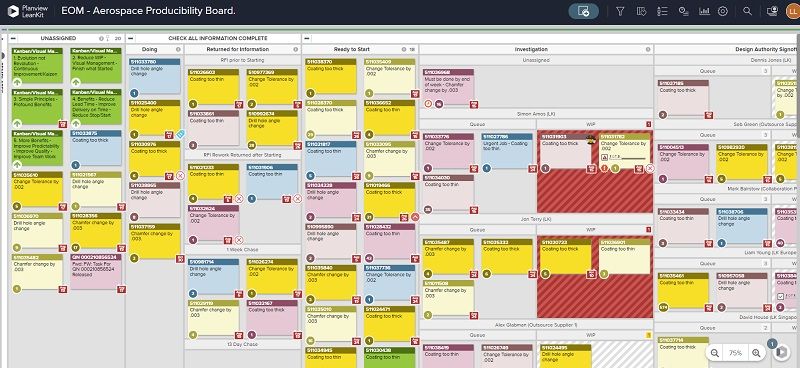
Visualization is an important concept in Lean manufacturing: Visualizing how value flows through an organization can help teams identify opportunities for improvement.
Kanban is a helpful, practical approach to workflow management. Managing your team’s work on a Kanban board will help you see where bottlenecks and blockers occur, where you have capacity issues, and where work gets stuck – allowing you to practice continuous improvement at every level.
Limites WIP
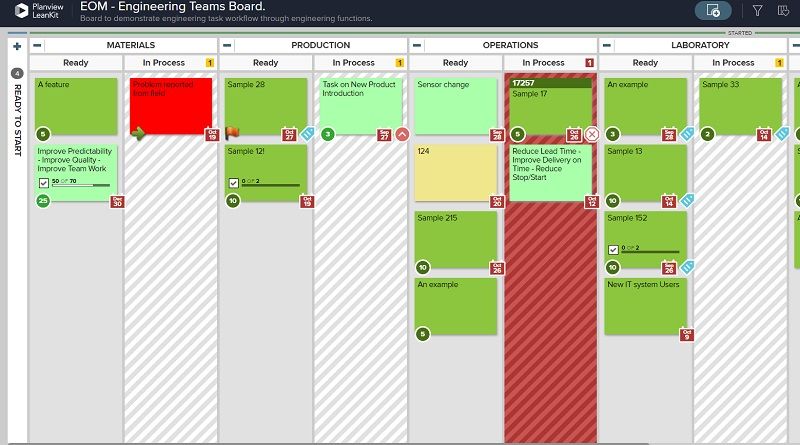
Achieving a state of continuous flow is the goal for any Lean organization – consistently, steadily delivering value to customers. Lean teams do this by actively managing their capacity – doing less at once and being more intentional about what they’re doing.
WIP limits (work-in-process limits) are fixed constraints, typically implemented on Kanban boards, that help teams quantify and manage capacity. WIP limits can help teams identify, then reduce or eliminate the most common sources of process waste, so they can more effectively deliver value to their customers.
Implementing WIP limits at every level of the enterprise is an important step in implementing Lean manufacturing.
Continuous Delivery
Continuous delivery describes a system with a sustainable and continuous flow of work. While continuous delivery isn’t our number-one goal, it can help us achieve our goal of creating more value for our customers.
Optimizing for continuous delivery means that we make decisions to break work down into smaller chunks and aim to move those chunks through our process quickly and efficiently.
Doing so allows us to get value into the hands of our customers faster, which helps us learn, grow, and adapt faster than our competitors. This is especially important for manufacturers of large-scale products, for which cost of delay is measured in millions of dollars per day.
Aiming to practice continuous delivery, ideally through the use of Kanban boards and WIP limits, is an excellent way to increase speed and gain momentum in a company looking to undergo a Lean transformation.
Pull System
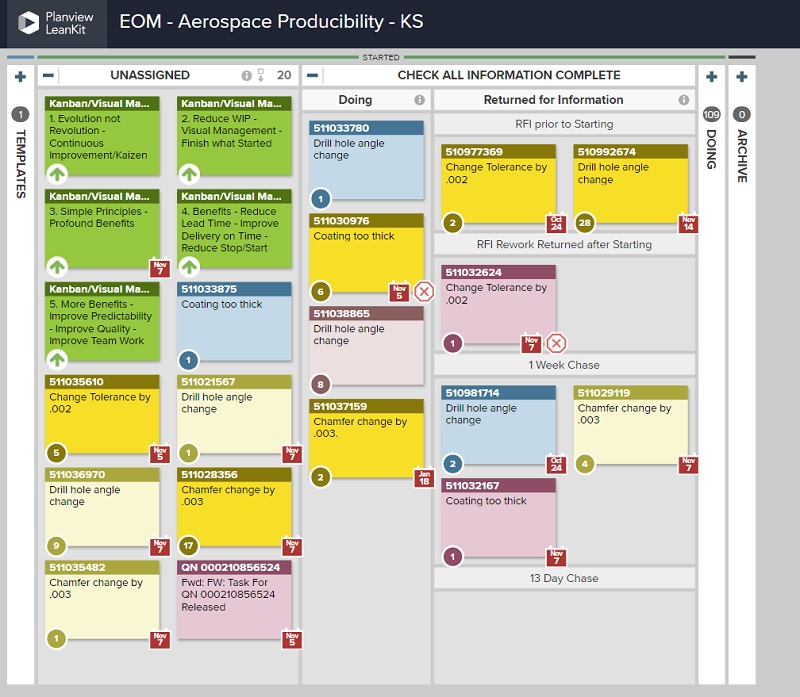
In most work systems, work is pushed from one person to another – employee A finishes a piece of work and then throws it over the wall to employee B. The problem with this system is that it’s hardly a system at all, since the team works without respect to each other’s capacity or current workload. Flow issues such as bottlenecks, blockers, etc. are likely to occur, draining the morale and efficiency of the team.
We learned earlier that Lean teams aim to optimize the whole. One practical way we do this is by using a pull system. Rather than blindly starting work and pushing it onto our coworkers, we first try to help coworkers finish existing tasks before starting new ones. When all opportunities to assist with existing work have been exhausted, we can pull new work onto the board. If we are responsible for the first step on a project, we don’t push it onto our coworker when we’re done. We notify them when it’s ready, and then they pull it into the next step when they have capacity for it.
This might seem like a minor distinction, but using a pull system can have a dramatic impact on a team’s productivity, efficiency, and morale.
Amélioration continue
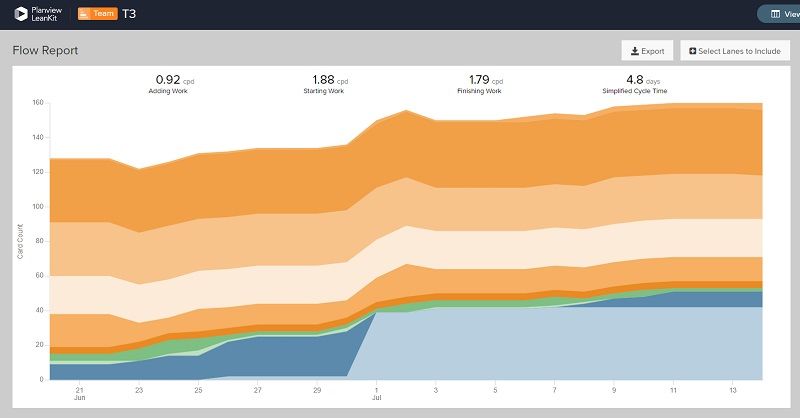
Every Lean manufacturing implementation is different; some begin as grassroots movements while others start from the top-down. Some extend to all functions of a business while others are limited to manufacturing-oriented departments within an organization.
Regardless of how Lean gets started in your organization, it has the potential to make a significant impact on efficiency, productivity, innovation, and the bottom line.
By providing the structure to keep teams focused on efficiency and flow, the principles of Lean manufacturing not only help teams perform at a higher level, they’re also making manufacturing companies more attractive places to work for talented engineers.
We always recommend that any implementation of Lean manufacturing begins slowly and intentionally. Failed implementations are almost always due to a shallow understanding of Lean basics. But if you can align around your why – and then share Lean thinking and principles across your organization – you have everything you need to launch a successful implementation of Lean manufacturing.